Planifica mejor tus rutas en chile
Plan and optimize your routes in seconds.
tus rutas en segundos

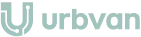
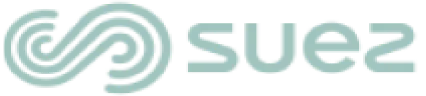
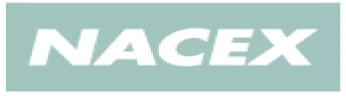

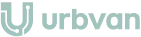
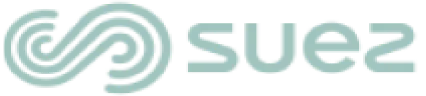
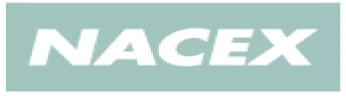

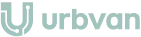
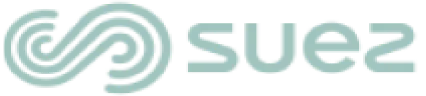
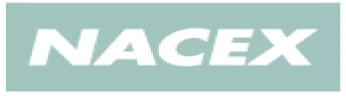

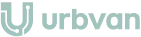
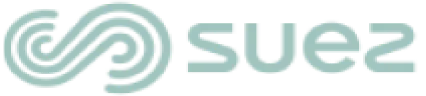
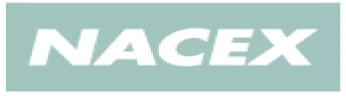
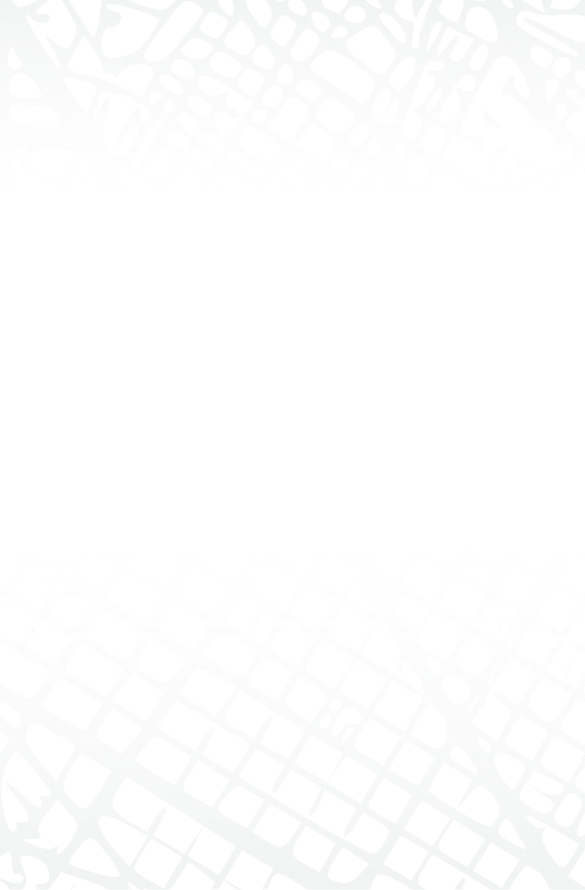
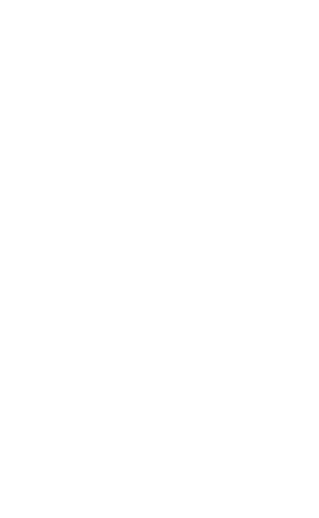

Automate all your last-mile processes
You'll have all the parameters you need to give you the best results instantly.
Finally a simple planner that you can use today.
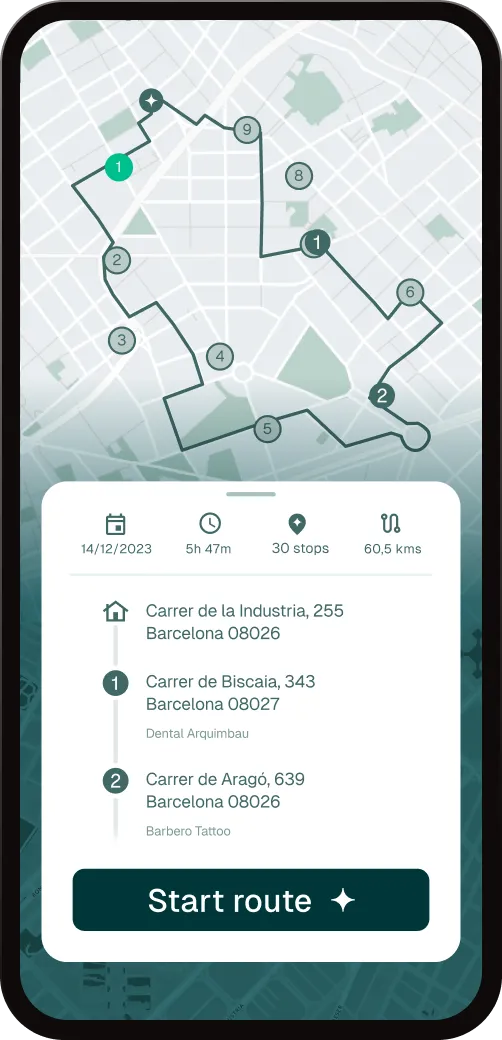
The drivers they only need a cell phone and internet access.
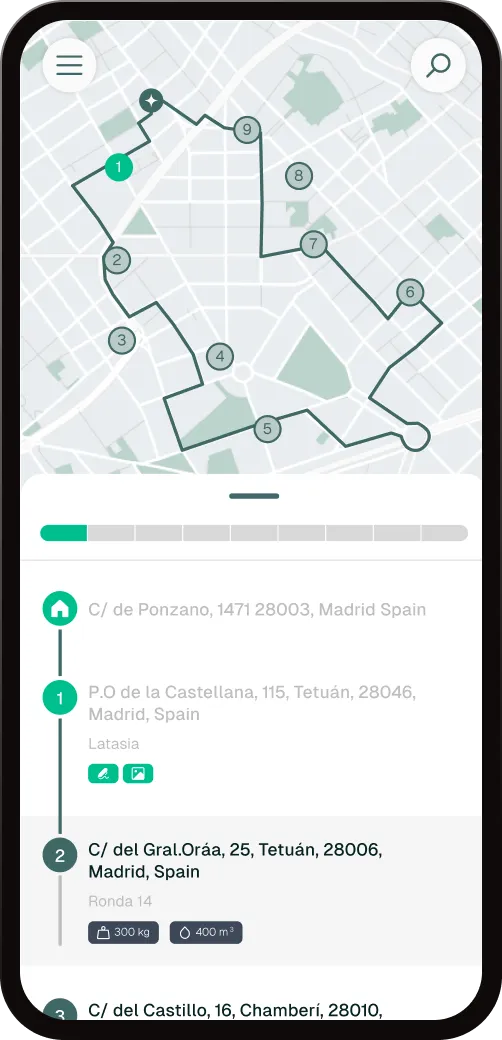
Raise the customer experience.
Precise updates.
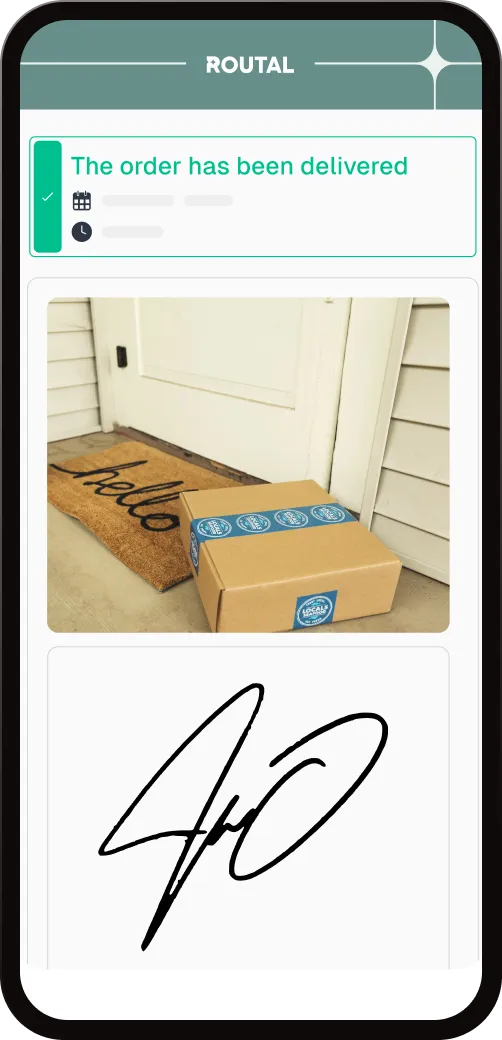
We help large and small companies in
. Thank you!










Optimize your routes in 3 clicks
Success stories, transformative results.
Our latest news and industry know-how.
%20(9).webp)
In an increasingly competitive environment, logistics has ceased to be an operational function to become a strategic axis of the business. The efficiency with which a company manages its deliveries, routes and resources directly impacts profitability, customer satisfaction and the ability to scale.
Therefore, it is no longer enough to leave logistics in the hands of the corresponding department: CEOs must be aware of and closely follow certain key indicators, especially in sectors where distribution is an essential part of the value proposition.
In this article we review the 5 logistics metrics that every CEO should have on their radar to align strategic decisions with operational reality. With solutions such as Routal, it is not only possible to measure these indicators in real time, but also to act on them to gain efficiency, reduce costs and provide a better service.
1. First installment success rate
La first effective delivery is one of the main indicators of efficiency in the last mile. If the order is not delivered on the first attempt, costs skyrocket: time is wasted, more fuel is consumed and customer dissatisfaction is generated.
A low success rate in the first delivery is often due to poor planning or poor communication with the customer. Routal Planner makes it possible to improve this ratio by:
- Automatic notifications with estimated time of arrival.
- Flexible selection of time slots.
- Real-time tracking information.
A CEO must keep this KPI under control to ensure that the delivery promise is fulfilled without additional costs.
2. Logistic cost per order
This indicator measures the direct economic impact of each logistics operation. It includes transportation, personnel, fuel, infrastructure and tool costs. If this value grows without increasing sales or complexity, there is an efficiency problem.
Measuring the cost per order allows:
- Identify oversized routes.
- Detect inefficiencies in resource allocation
- Evaluate the ROI of new logistics investments.
With Routal, you can reduce this cost by planning shorter routes, avoiding failed deliveries and making better use of each delivery day.
3. Logistic Service Level (OTIF)
The OTIF KPI (”On Time In Full”) measures how many orders are delivered On time and in full, as promised. It is a critical metric for understanding if logistics is fulfilling its strategic function.
A low OTIF score indicates failures that impact:
- Customer Satisfaction.
- Repeat purchase rate.
- Brand image.
Routal technology makes it possible to improve this indicator through real-time visibility, precise planning and agile reactions to unforeseen events.
4. Average delivery time
This metric allows us to know How long does it take for your company to deliver an order since it is generated. It is vital to evaluate the capacity to respond to demand and to optimize processes.
A CEO should keep an eye on whether the average delivery time:
- It is aligned with market expectations.
- It is improving compared to the competition.
- It is affected by internal bottlenecks.
Thanks to Routal's automatic route optimization, many companies have been able to reduce this time without the need to expand their fleet or staff.
5. Logistic capacity used
Having a large fleet or many hours of work available does not guarantee efficiency if are not being used properly. This metric measures the degree of effective use of logistics resources (vehicles, delivery people, warehouses).
Low utilization means wasted fixed costs. Excessive utilization can lead to operational fatigue and errors. Routal helps balance loads, optimize shifts and redistribute routes to maximize performance without overtaxing the team.
What is not measured, cannot be improved
A CEO doesn't need to know all the details of daily operations, but he should have visibility over key logistics indicators. The best strategic decisions start from rigorous data analysis that reflect the reality of the business.
Tools such as Routal they make it possible to turn logistics into a source of competitive advantage: beyond planning routes, they offer you operational intelligence to reduce costs, improve customer experience and scale solidly.
Do you have these metrics under control? If not, perhaps it's time to transform your logistics into a strategic pillar with the help of technology.
%20(8).webp)
Managing a fleet of vehicles doesn't just mean coordinating routes or keeping logistics operational. It also has a direct impact on the company's financial results. To know if you're managing your resources well and if your decisions are aligned with profitability objectives, you need more than intuition: you need data.
In this article we are going to review the 5 key financial indicators to evaluate the performance of your fleet. Not only do these KPIs help you to have a clear view of costs, but they also allow you to identify hidden inefficiencies and opportunities for improvement. And the best part: you can control them in real time with a solution like Routal, which turns your logistics operations into a constant source of useful data for making more profitable decisions.
Because when it comes to financial efficiency, what isn't measured, can't be improved.
1. Cost per kilometer (CPK)
This is one of the most basic and, at the same time, the most revealing indicators. El cost per kilometer represents how much it actually costs you to move your fleet for each kilometer traveled, taking into account fuel, maintenance, salaries and amortization of the vehicle.
A high CPK can be a sign of poorly optimized routes, inefficient vehicles, or lack of preventive maintenance. With Routal Planner, you can significantly reduce this indicator by generating shorter routes and avoiding unnecessary detours.
2. Fleet occupancy rate
Are your vehicles driving with a full load or traveling half empty? La occupancy rate shows you the percentage of capacity used compared to the total available. An underutilized fleet means more trips, more costs and less efficiency.
Intelligent planning allows you to optimally group orders and assign the right vehicle for each route. This maximizes the use of each unit and avoids redundant costs, such as using large trucks for small deliveries.
3. Cost per delivery
This KPI is essential to understand if your distribution model is profitable. El cost per delivery is calculated by dividing total operating costs by the number of deliveries made in a period. If this value goes up, you're probably having planning failures, failed deliveries, or oversized routes.
Automating routes and time windows What Routal offers reduces downtime, assignment errors and first delivery failures, which directly translates into a lower cost per delivery.
4. Costs per vehicle per day
Beyond the cost per kilometer, it is important to know how much it costs to have each vehicle in operation on a daily basis, even if it is not at 100% capacity. This indicator includes insurance, depreciation, maintenance and associated fixed costs.
If a vehicle spends more time standing than operating, its real daily cost skyrockets. With a tool like Routal, you can balance the load between vehicles and make decisions about fleet renewal or downsizing with solid economic criteria.
5. Failed delivery rate
Each delivery that is not completed generates a additional hidden cost: second attempt, delivery time, extra fuel and, in many cases, loss of reputation. A high failed delivery rate has a direct impact on profits.
Minimizing this indicator requires proactive planning, communication with the customer, and real-time visibility. Routal allows you to send automatic notifications, provide delivery tracking and agile rescheduling in case of unforeseen events. This not only improves the KPI, but also the customer experience.
Measure, Adjust and Improve
Controlling these five financial indicators isn't just a task for the accounting department: it's a strategic tool for making better logistics decisions. If you don't measure how much each kilometer, delivery or vehicle costs, You're managing blindly.
A solution like Routal allows you not only to plan more efficient routes, but also to visualize in real time the economic impact of each movement of your fleet. With this data in hand, you can reduce costs, improve margins and transform your logistics into a true engine of profitability.
Do you want to start measuring what really matters in your operations? Discover How Routal can help you to make decisions based on data, not assumptions.
%20(7).webp)
The last mile is one of the most expensive and complex sections of the entire logistics chain. Although the costs of this phase are often associated with fuel, personnel or vehicles, there are numerous hidden costs that have a silent but direct impact on the profitability of companies.
Cumulative delays, failed deliveries, poorly designed routes or unplanned waiting times generate invisible losses that add up day after day. And the most worrying thing: they tend to go unnoticed until they result in customer complaints, logistical overruns or reduced margins.
In this article we analyze what those are hidden costs in the last mile, why they occur and how you can avoid them. You'll see how an intelligent planning tool like Routal can help you identify these mismatches and optimize each delivery, saving time, money and frustration. Because A poorly managed last mile not only costs more, it also affects the customer experience.
The problem: costs you don't see, but you do pay
Many logistics managers believe they have delivery costs under control because they know the price of fuel, the salaries of the delivery people or the maintenance of the fleet. However, Most of the relevant last-mile costs don't show up in traditional spreadsheets. They're harder to measure, but they have a real impact.
Some common examples:
- Delays due to inefficient routes, which increase the total time of each day.
- Waiting times at delivery points, especially when the customer is not available.
- Failed or rescheduled deliveries, which involve double work and more kilometers.
- Poorly informed manual decisions, which generate logistical errors or overlaps between routes.
- Lack of real-time visibility, which prevents reacting to unforeseen events or redistributing tasks in an agile way.
These factors cause a cumulative loss that often goes unnoticed. And the most worrying thing: directly affect customer satisfaction, causing complaints, returns or even loss of loyalty.
In short, without efficient, data-based planning, last-mile operations become more expensive, less predictable, and much more difficult to scale.
How to reduce hidden costs with efficient planning
The good news is that most of these invisible costs can be significantly reduced through a more intelligent planning strategy, based on data and supported by technology. Here are the keys to achieving this:
Real-time route optimization
The first step in reducing cost overruns is to have a tool that generate efficient and adaptable routes. Routal Planner allows you to create itineraries taking into account multiple variables: traffic, road restrictions, order priority, type of customer or load capacity.
Thanks to this optimized planning:
- Kilometers traveled and fuel consumption are reduced.
- Transit time between stops is minimized.
- Common problem areas or bottlenecks are avoided.
All of this translates into more profitable days and faster deliveries, without the need to expand the fleet or equipment.
Reduction of failed deliveries and reattempts
Each delivery that is not completed the first time generates a double hidden cost: re-planning and moving again. To avoid this, it is key to:
- Notify the customer in advance of the estimated time of arrival.
- Offer the possibility to choose the most convenient time slot.
- Allow last-minute changes from an online portal.
Routal technology allows you to automate all these communications, facilitating coordination and reducing failed attempts. This not only saves costs: improves the customer experience and reduces operational stress.
Elimination of downtime
Waiting times and non-productive downtime are often among the most invisible and frequent costs. By not having visibility into what is happening at each delivery point, many companies accumulate Avoidable downtimes.
With Routal you can:
- Monitor the progress of each route in real time.
- Detect if a delivery person is stuck or has had an incident.
- Reassign deliveries on the fly so as not to lose efficiency.
This allows for a much more agile operation, in which every minute of work is used to the maximum.
Prioritization of strategic deliveries
Not all orders generate the same value. A delivery to a key customer, an express delivery or a perishable merchandise should be given preference over other, less critical shipments. However, many companies continue to plan all deliveries with the same logic.
Advanced planning such as that offered by Routal allows:
- Assign automatic priority levels.
- Order routes to maximize business impact.
- Avoid errors due to uninformed manual decisions.
This translates into fewer incidents, better use of resources and a service that is more aligned with business objectives.