Planifica mejor tus rutas en LATAM
Plan and optimize your routes in seconds.
tus rutas en segundos

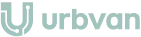
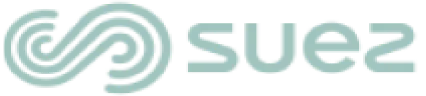
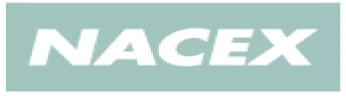

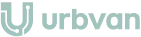
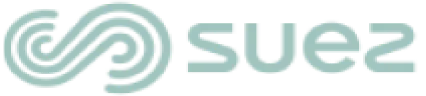
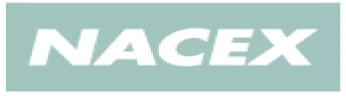

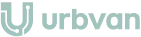
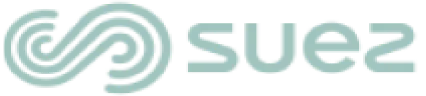
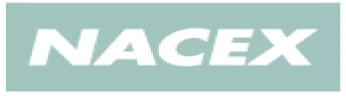

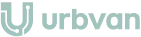
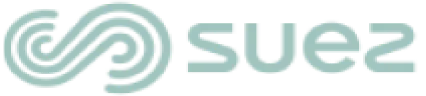
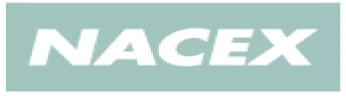
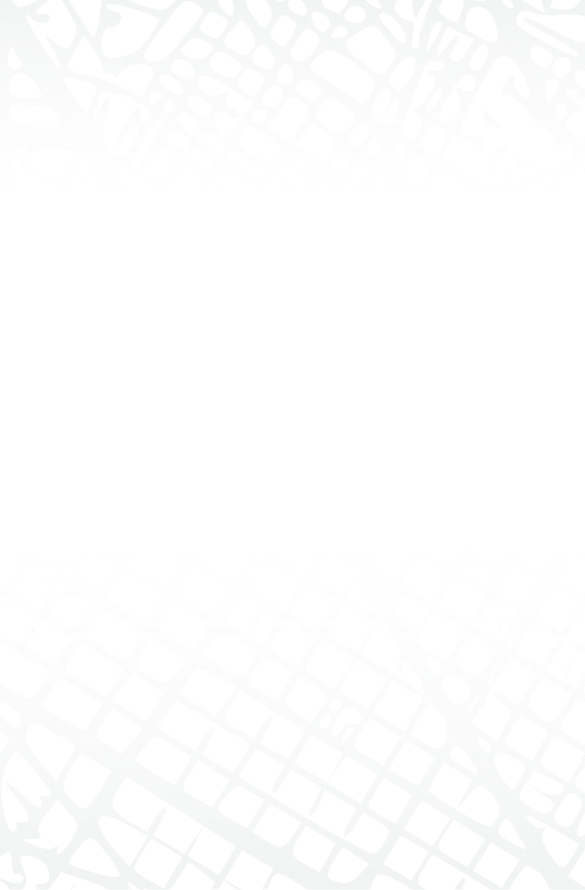
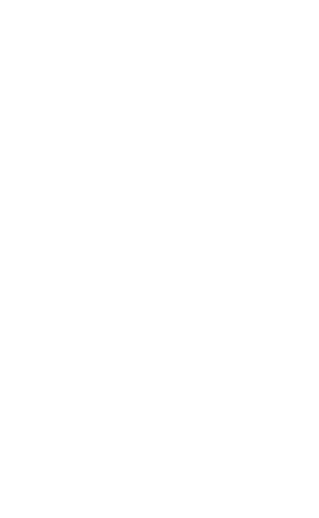

Automate all your last-mile processes
You'll have all the parameters you need to give you the best results instantly.
Finally a simple planner that you can use today.
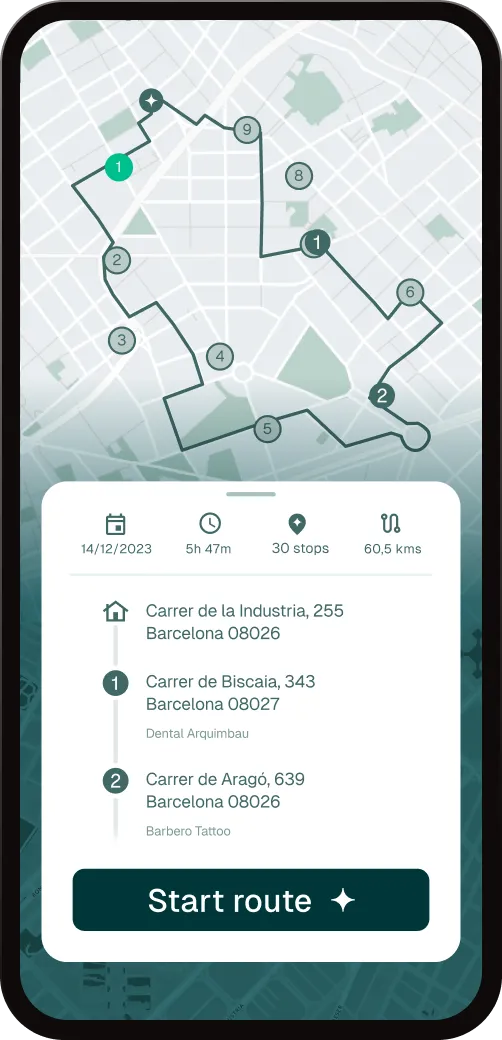
The drivers they only need a cell phone and internet access.
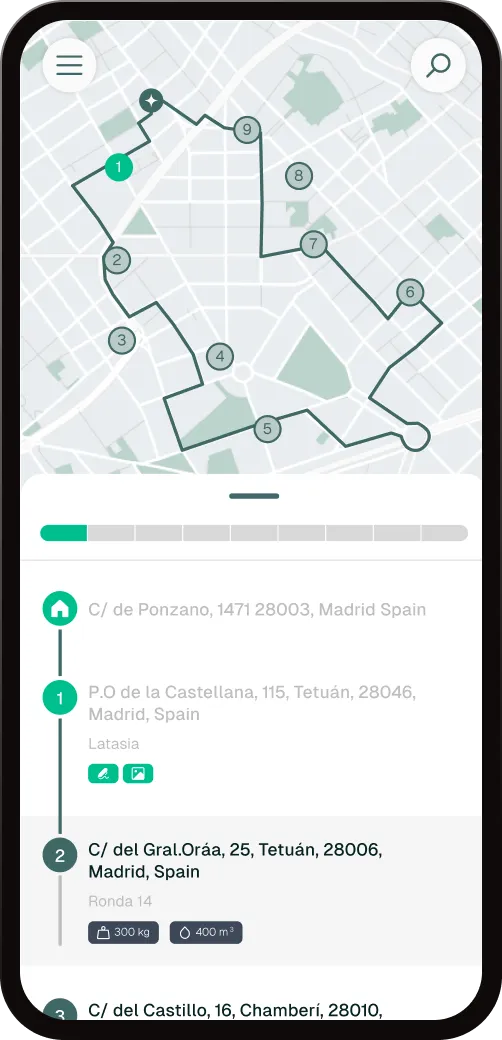
Raise the customer experience.
Precise updates.
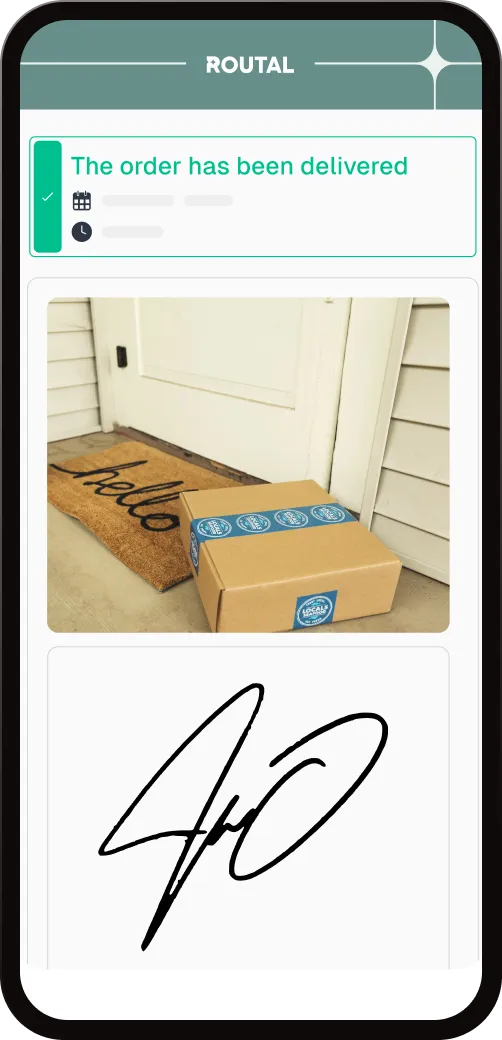
We help large and small companies in
. Thank you!










Optimize your routes in 3 clicks
Success stories, transformative results.
Our latest news and industry know-how.
%20(2).webp)
Modern logistics is no longer based solely on prior planning. Each delivery is exposed to unpredictable factors: traffic, last-minute changes, weather conditions or unforeseen events with the customer. In this context, the artificial intelligence (AI) has become a key element in anticipating problems and making faster and more accurate decisions.
Using predictive models, machine learning and real-time data analysis, companies can Anticipate delays before they occur, dynamically optimize routes and adjust your operations on the fly. This ability to react directly transforms operational efficiency, reducing costs and improving the customer experience.
In this article, we explore how AI is redefining logistics, what specific applications it offers and how tools such as Routal integrate these technologies to offer a competitive advantage to delivery and distribution companies.
What does AI bring to last-mile logistics?
Artificial intelligence allows companies to move from reactive logic to a proactive approach. Instead of waiting for a problem to arise, algorithms can detect patterns that anticipate incidents. This translates into a greater capacity to prevent delays, redistribute resources and maintain control of the entire logistics operation.
Among their most valuable contributions are:
- Delay prediction based on historical and variable data in real time.
- Identifying optimal alternative routes, depending on traffic, weather or urban restrictions.
- Automatic replanning when deviations are detected in the expected times.
- Intelligent delivery prioritization, adapted to the type of customer or level of urgency.
How does predicting delays with AI work
AI is nourished by a large amount of data: historical routes, service times, past incidents, traffic data, weather conditions, etc. Based on these inputs, machine learning models generate predictions that allow anticipate when and where delays could occur.
For example, if a delivery has been delayed four previous times in the same time zone and geographical area, the AI identifies it as a risk point and can adjust the route before it happens again.
On platforms such as Routal Planner, this functionality translates into automatic alerts for planners, to quickly identify delays and to be able to make quick and proactive decisions in the face of unforeseen events.
Use Cases: Agile Decisions in Complex Environments
1. Real-time route replanning
When a delivery person is delayed or blocked due to an incident, AI can automatically replan routes, avoiding bottlenecks and improving compliance with schedules.
2. Prioritization of critical deliveries
Based on customer behavior patterns, AI can identify which deliveries are most sensitive to delay (for example, a supermarket with high turnover or a VIP customer), and Adjust the order of distribution to ensure their punctuality.
3. Optimizing resources
In addition to improving routes, AI also helps to plan the exact number of vehicles and drivers needed, reducing excessive use of resources and adjusting shifts to real demand.
Competitive advantages of applying AI in logistics
Companies that integrate AI into their logistics operations obtain clear benefits:
- Greater reliability in deliveries, even under unforeseen conditions.
- Reduction of operating costs, by avoiding inefficient routes and intelligently reorganizing resources.
- Decrease in operational stress, since planners don't have to manually resolve each issue.
- Improving customer satisfaction, by providing more accurate information and fulfilling delivery promises.
In addition, having AI-based technology is key to scaling the operation without the need to multiply the human team.
Routal: AI integrated into every logistics decision
Routal has developed a planning system that combines predictive algorithms, data analysis and real-time monitoring. This allows companies to react before problems turn into logistical failures.
Thanks to its artificial intelligence engine, Routal offers:
- Automatic alerts for deliveries with a risk of delay.
- Instant reassignment of orders to avoid non-fulfilment.
- Alternative route suggestions that take into account traffic, restricted areas or weather conditions.
- Control panels that show operational status and possible incidents in real time.
All of this allows teams to make faster, more informed and accurate decisions.
From manual control to intelligent logistics
Modern logistics requires agility, precision and adaptability. With the help of artificial intelligence, companies no longer need to wait for a problem to appear before taking action: they can anticipate, adapt and continuously improve.
The integration of technologies such as Routal Planner allows you to automate critical decisions, reduce uncertainty and provide a more reliable delivery experience. Betting on AI is not a fad, but a key strategy to stay competitive in a market where every minute counts.
%20(1).webp)
Designing efficient delivery routes is no longer just a matter of arriving fast. Today, companies are faced with the challenge of optimizing their operations considering multiple variables at the same time: minimize delivery times, reduce logistics costs and maintain a firm commitment to sustainability. Is it possible to achieve that balance? The answer is yes, but it requires strategy, technology and a mindset aimed at intelligent efficiency.
In this article, we explain how companies can integrate these three factors —weather, cost and sustainability— in a realistic and scalable route planning model. In addition, you'll see how tools like Routal Planner facilitate this process with automation, real-time data and advanced optimization algorithms.
The pressure to deliver faster without increasing costs or polluting more is transforming logistics. Here you'll discover how to adapt without giving up on any goal.
Why is a multi-criteria approach necessary in route planning?
Traditionally, many companies have designed their logistics routes prioritizing only the shortest possible delivery time. However, this strategy ignores other key elements that directly impact the profitability and environmental responsibility of the operation.
An approach Multicriteria allows you to take into account variables such as:
- Time of delivery, to ensure punctuality and improve the customer experience.
- Operating costs, including fuel, working hours and vehicle wear and tear.
- Sustainability, with routes that minimize emissions and reduce the number of kilometers traveled unnecessarily.
Balancing these factors isn't easy manually. This is where technology comes in as a key ally.
Technology applied to intelligent planning
A solution such as Routal enables automatically design routes based on multiple simultaneous objectives. The system analyzes variables such as:
- Delivery time windows requested by the customer.
- Traffic restrictions or real-time conditions.
- Location and capacity of each vehicle.
- Geographical distribution of deliveries.
The result is a plan that prioritize efficiency without sacrificing sustainability. Thanks to optimization algorithms, each route is evaluated for its total impact, not just speed.
Practical strategies for balancing time, cost and sustainability
1. Intelligent grouping of deliveries
Grouping deliveries close geographically allows you to reduce kilometers traveled, minimize stops and improve energy efficiency. It's a simple but very powerful tactic when combined with automatic planning systems.
2. Use of Key Indicators (KPIs) for each objective
Balance can only be maintained if it is measured continuously. Some key metrics include:
- Average delivery time.
- Cost per kilometer.
- CO₂ emissions per completed route.
Routal allows you to monitor these KPIs in real time to adjust the strategy when necessary.
3. Inclusion of environmental variables
Many cities already impose restrictions on polluting vehicles. Designing routes that avoid restricted areas or that prioritize less polluting vehicles allows not only to comply with regulations, but position the brand as socially responsible.
4. Dynamic replanning for unforeseen events
Traffic, delays or customer absences are inevitable. A system like Routal can reoptimize routes on the fly, avoiding bottlenecks and ensuring that the rest of the operation is not affected.
Concrete benefits of multi-criteria planning
Companies that have adopted this model report benefits such as:
- 15-25% reduction in operating costs, thanks to shorter and more efficient routes.
- Reduction of emissions by up to 30%, combining better planning and sustainable vehicles.
- Improved NPS (Net Promoter Score) for more timely and accurate deliveries.
In addition, greater satisfaction is achieved from logistics teams, who work with less pressure and better information.
Result: Efficiency with purpose
Designing multi-criteria delivery routes is no longer an option, but a necessity for any company that wants be competitive, profitable and responsible. Balancing time, cost and sustainability is possible thanks to specialized tools such as Routal Planner, which integrate data, automation and the ability to react in real time.
Adopting this model not only improves the logistics operation. Also strengthens brand reputation, generates medium-term savings and prepares the company to respond to the new demands of the market and the planet.
.webp)
What if I told you that your route planning with Excel could be holding back your growth?
Yes, we know it works.
But we also know that it leaves a lot of room for error ❗
Do these cases ring a bell to you?
• Miscopied cells that alter the entire cast
• Drivers calling because they don't understand the order of deliveries
• Customers upset by avoidable delays
All of this is more common than it seems.
And it's not because there's a lack of effort, but because Excel wasn't designed for logistics management.
💡 When we use generic tools for critical processes, we pay for it in time, money... and headaches.
On the other hand, a specialized route software how Routal automates what you now do manually:
✓ Generate optimized routes in seconds
✓ It is updated in real time in the event of unforeseen events
✓ Share routes with your drivers and customers in one click
The result?
📉 Fewer errors
📈 More deliveries in less time
😊 And a much quieter team
The best part: you don't need to be a logistics expert or hire an engineer.
Routal adapts to your operation and scales with you.
And hundreds of companies like yours are already using it to leave logistics management behind with Excel.
👉 Find out how other companies like yours are automating it.
Does it happen to you too? Do you still rely on Excel for planning?